In the field of material cutting and precision shaping, two contrasting methods have emerged as industry leaders: waterjet cutting and traditional cutting methods. Each approach brings its own unique set of advantages and disadvantages, leading many people to consider which one is right for their specific needs. To make an informed decision, it is important to delve deeper into the intricacies of both waterjet cutting and traditional methods, considering factors such as accuracy, efficiency, material versatility, and environmental impact.
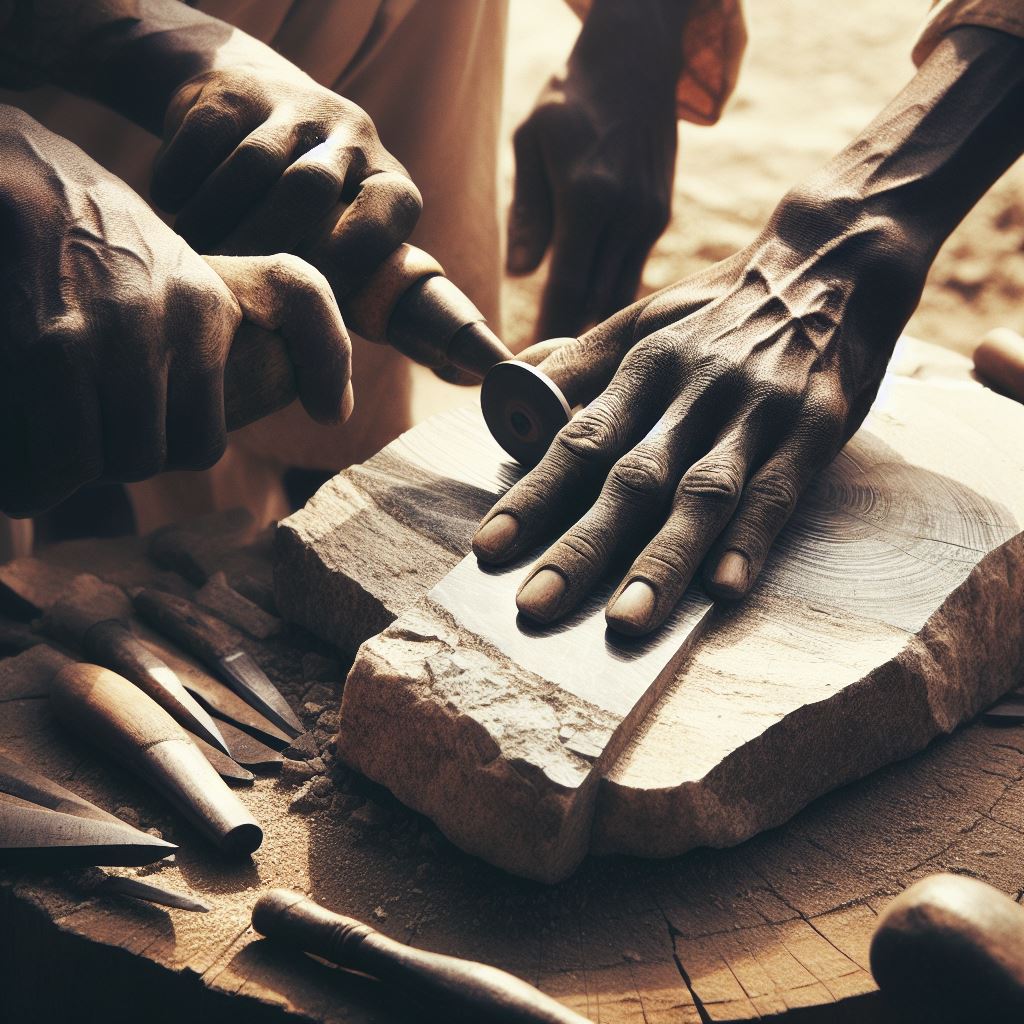
Traditional Cutting Methods
Traditional cutting techniques, such as sawing, shaving, and grinding, have long been the basis of material shaping. These methods rely on abrasive tools or heat to cut the material. Although they have a history of effective use, they come with some inherent limitations.
Pros:
- Familiarity: Traditional methods are well-established and widely understood, making them a go-to choice for many industries.
- Cost-Effective: These methods are often less expensive in terms of initial equipment and maintenance.
- Rapid Cuts: Traditional methods can provide quick results for simpler projects with basic shapes.
Cons:
- Material Limitations: Traditional methods are typically better suited for metals and simpler materials, and may struggle with intricate designs or more delicate substances like glass or plastics.
- Heat-Related Issues: Heat generated during traditional cutting can distort materials or cause thermal stress, potentially affecting the integrity of the finished product.
- Tool Wear: Traditional cutting tools often wear out quickly and need frequent replacements, increasing operational costs.
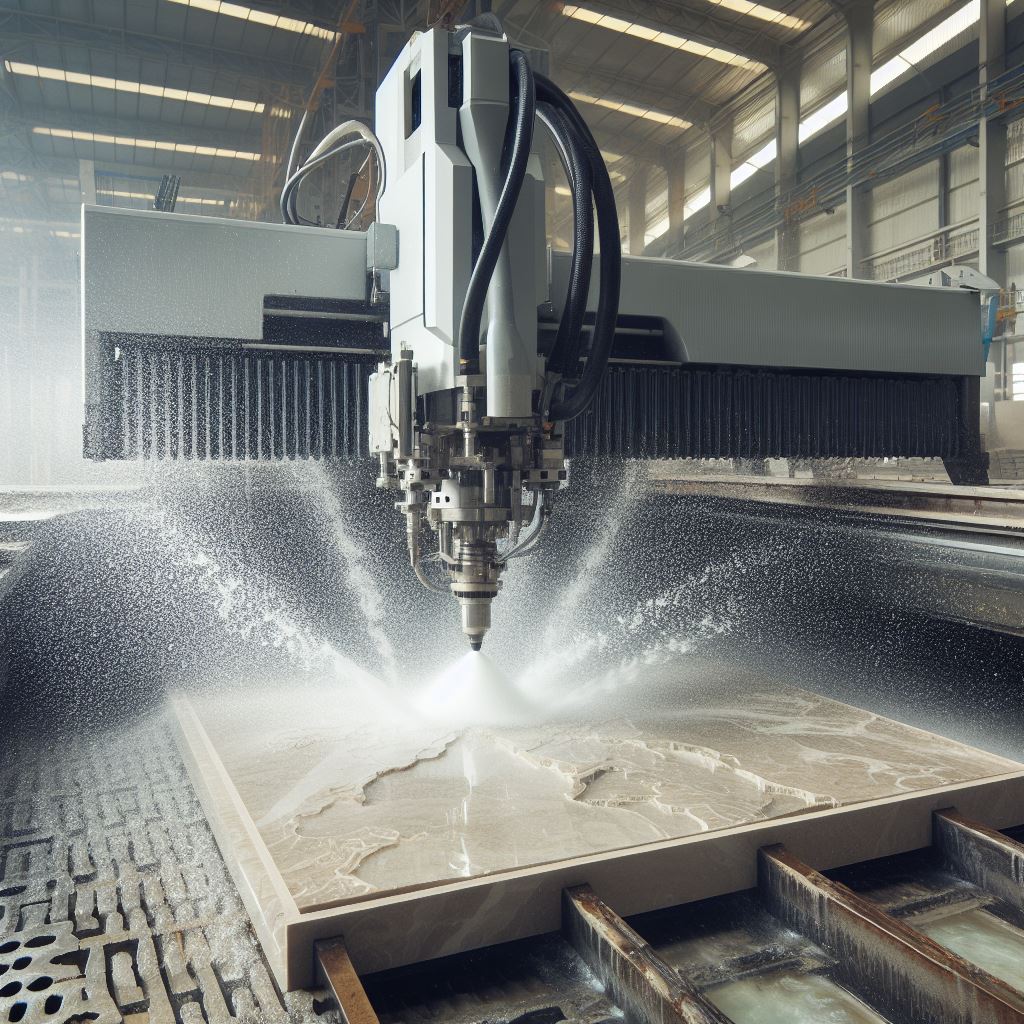
Waterjet Cutting
Waterjet cutting, on the other hand, is a more recent technology that utilizes a high-pressure stream of water mixed with abrasive particles to cut through materials. It has gained popularity due to its versatility and ability to provide precise and intricate cuts.
Pros:
- Versatility: Waterjet cutting is highly versatile, capable of handling a broad range of materials, including metals, ceramics, glass, plastics, and composites.
- Precision: Waterjet cutting offers exceptional precision and the ability to create complex shapes and patterns with ease.
- No Heat-Affected Zone (HAZ): Since waterjet cutting is a cold-cutting process, it doesn’t generate heat, minimizing the risk of material distortion or damage.
- Minimal Material Waste: Waterjet cutting minimizes material wastage, which can be especially valuable for expensive or limited-supply materials.
Cons:
- Initial Costs: The equipment and maintenance costs for waterjet cutting machines can be higher than those for traditional methods.
- Speed: While waterjet cutting provides precision, it may not be as fast as traditional methods for some applications.
- Maintenance: Waterjet machines require regular maintenance to ensure they function optimally.
Choosing the Right Method
The choice between waterjet cutting and traditional methods depends on your specific project requirements and priorities. If precision, versatility, and minimal material waste are your primary concerns, waterjet cutting might be the ideal choice, especially for industries like aerospace, architecture, and high-precision manufacturing. Traditional methods still have their place, particularly in situations where cost-effectiveness or speed is the top priority.
In conclusion, when it comes to choosing between waterjet cutting and traditional methods, it’s essential to assess your project’s unique needs, materials, and budget. Both approaches have their advantages, but understanding the nuances of each will help you make an informed decision that ensures optimal results for your cutting and shaping projects.
Add a Comment